Takt time, Cycle time and Lead time are 3 notions that are interconnected. Initially, we’ll present each one separately, to better understand what each one means. Further, we’ll present practical examples to clarify the connections between them.
Also, you can download a free Takt time calculator, as well as a free Cycle time calculator.
Takt time
The optimal pace to meet customers’ demands
What is takt time
Takt time is the concept that defines the optimal production rate for an item, so as to meet customer expectations. So, the unit of measurement for Takt time is seconds per unit.
A simple example:
If you have a hotdog cart, and you work 8 hours/day, and you have 80 customers. Hence, that means that you must prepare 10 hotdogs each hour = 1 hot dog every 6 minutes. So, your takt time is 6 minutes
480 minutes of work time / 80 hot dogs = 6 minutes / hot dog
This dimension is of utmost importance in the production lines. Especially when items go through multiple stations, where each of them performs a certain set of predefined tasks. But, in a business environment Takt time can be used on most tasks. For example, in administration, control tasks, or manufacturing.For instance, if not properly adjusted, one of the two situations may occur:
- Takt time faster than needed.
This situation determines producing ahead of demand and specific problems will arise. For example, will have negative implications on costs related to the storage of production. Also, may determine premature procurement of raw materials, or lack of production for other necessary items. - Takt time slower than needed.
In this case, the first and most important negative effect is customer dissatisfaction. As a result, the implications of this fact are immediately reflected in the subsequent decrease in sales. Besides, the solutions that will need to be applied in this situation will cause additional costs. For example, these can be linked to overtime work to complete production or urgent transportation.
Takt time may be adjusted according to various factors. To illustrate, we can list requirements within the company, daily working time, downtimes on machines. But, once settled, the production needs to be executed within the established takt-time. Therefore, measures will have to be taken immediately. For instance, supplementing the resources or adjusting the demand or even rethinking the production process.
Takt time formula
The elements that are taken into account when applying the Takt time formula are the following:
- Average daily customer demand for the item
- Total available working time per day, expressed in seconds
The takt time formula is
Tt = Wt / D
This means the Total available working time per day (seconds) divided by the Average daily customer demand for the item.
Noteworthy: the Total available working time per day will be expressed in seconds.As formulated above, the Total available working time per day means net working-time. Therefore, lunch breaks, meetings, or interruptions caused by unscheduled downtime are not included. So, the Total available working time per day that will be included in the Takt time formula, results from the following calculation:
(the number of shifts per day x the number of seconds per shift) – (scheduled breaks + average daily setup and maintenance time + average daily unscheduled downtime)
Takt time calculation
Takt Time calculation is the most important factor that shows whether you can keep up with your customer demand.
For this reason, it is very important to decide from the beginning whether to include, or not, some estimated downtime.
- If not included in the calculation but still happen, then these interruptions will cause a drop in production
- If included in the calculation and it does not happen, then the output will be higher than planned
Anyway, in both situations, it is necessary to take measures that will adjust the effects and that will cause additional costs.
Of course, production with perfectly stable processes and completely balanced flow would be the ideal situation.
However, in practice, it is almost impossible to avoid unforeseen situations.
For this reason, the calculations can take into account an estimated average time of possible interruptions.
Benefits of Takt time
- helps to create a strategic scheduling
- raise awareness of production rates
- highlights possible problems
- balances production
- prevents buildups of inventory
Cycle time
An essential metric in productivity that focuses on the measurement of work done
Cycle time definition
For Cycle time definition there are several variants and they can all be correct considering the variables involved. Thus, in production the definition refers to the average amount of time for the full execution of an item.
Therefore, this period starts when the procedure of production begins and it ends when the item is complete.Note the difference between the definitions of the 3 notions:
- Takt refers to the actual time that it takes to complete your item
- Cycle represents the rate at which each item must be executed so that the production meets the client demand
- Lead is about the total time elapsed from the taking of the order to the delivery
Cycle time formula
If we take into account the Cycle time definition, the Cycle time formula is very simple and clear:
End Date – Start Date = Cycle Time
This calculates the actual working time for the realization of an item. Therefore, it has to be measured from the beginning of the working process to the completion of the itemBut, in the same respect, another approach can be applied, namely:
Cycle Time = Net Production Time/Number of Units madeThis formula involves:
- counting runtime
- excluding non-working times
- dividing it by the number of units performed during that time interval
To begin with, an important thing to take into account is the non-working time. So, are these hours included or not included in the Cycle time formula?
In most cases, Average Cycle time is calculated therefore also an average amount of non-working hours are included. Also, for an exact calculation it is recommended to exclude non-working hours. However, this should also be done depending on how the other two “ times” are calculated.
The connection between Cycle time and Trakt time
However, it would be ideal for these two times to be equal, to have the same duration. As a result, this would mean that the production executed is in perfect compliance with your client’s demand. But, in practice, things are unlikely to happen that way. Therefore, we will also encounter situations such as:
- Cycle Time is less than Takt Time and this results in greater production than necessary
- Cycle Time is more than Takt Time which means that production cannot keep up with the necessity
Moreover, both situations create additional problems and costs. Consequently, during the production process, the balance between the two must be always maintained as good as possible.
The connection between Cycle time and Lead time
Cycle time is a vital component of Lead time. Consequently, the better the Cycle time, the better the Lead time. Also, taking into account that the three components are interconnected, we come to the conclusion that:
The more realistic is the Takt time set and shorter the Cycle time, the better the Lead time will become. Consequently, this will lead to guaranteed customer satisfaction, which is always a goal in business.
Lead time
The concept between a process initiation and completion
Lead time definition
A general Lead time definition is the elapsed time from the initialization to the completion of a process. Consequently, in addition to the production process itself, Lead time definition also includes other time intervals.
- One of these is the time elapsed from the moment the order was received until the start of its execution. The other is the time that elapses from when the production was completed until the product reaches the customer.
- Accordingly, Lead time is a notion that can include all the processes of an organization, not just the production.
Lead time meaning
Depending on the industry in which it is applied, Lead time meaning may be different.
In project management
Lead time meaning is related to all the independent or interdependent tasks within the same project.
In journalism
It includes all the time elapsed from when the subject was received until the delivery of the article.
In supply chain management
It goes from issuing the order to the supplier until the goods are delivered. Therefore, by taking into account:
- the amount of time needed to replenish your supply (supply delay)
- the time until you can place a reorder of supplies (reordering delay)
then we have a formula of Lead time for supply chain management:
Lead time = supply delay + reordering delay
In manufacturing
It includes the time required to
- confirm material availability
- prepare the documentation and plans
- consumed by preparing the products for delivery
Manufacturing also includes some other Lead time meanings. In particular, because each step from receiving the customer’s order to delivering it, can have its own Lead time meaning:
- Order Lead time (can be found in any supply chain management)
Start: receiving the order from the customer
Ends: when the products are received at the destination - Order Handling time
Starts: when the order is received from the customer
End: when the order is registered in the system - Manufacturing Lead time
Start: when the order is processed in the system
End: when the production is finished - Production lead time
Start: when the production process begins
End: with the completion of the production process - Delivery lead time
Start: when the production is completed
End: when the product is received by the client
Therefore, to calculate manufacturing lead time we’ll have to make the sum of all the elements included, which means:
Order Lead time + Order Handling time + Manufacturing Lead time + Production lead time + Delivery lead time
Interconnections
Lead time and especially its connections with the concepts of Takt time and Cycle time can greatly improve the efficiency of your activity and boost productivity.
For example, the Cycle time should be kept as close to Takt time as possible and Cycle time optimization will automatically lead to Lead time improvement.
Reducing Lead time improves productivity which automatically results in increased revenues.
Detailed step-by-step examples
Now that we know what each of the 3 different times means, let’s deepen the explanations with practical examples.
This will help you understand and design your processes in a more efficient manner. As a result, you will meet your customer’s demands better.
Takt time
As we said, this one is a value you have to calculate. It describes the rhythm at which you need to produce each item, to meet customer requirements. Thus, we may say that expresses the theoretical demand rate of your customer.
Takt time calculation involves dividing our available production time by the number of items our customer needs.
Takt time formula = available production time / the number of items ordered;
Example of Takt time calculation:
First, we’ll assume the following work schedule: 20 days a month, one shift a day, 7.5 hours a shift. In this situation, we will have an available production time of 150 hours, which means 540,000 seconds per month.
Available production time
7.5 h/day x 20 days a month = 150 h/month x 3600 sec/h = 540,000 sec/month
Second, let’s assume that the customer needs 20,000 items/ month. As a result, as we apply the Takt time formula, we will get 27 seconds per item.
Takt time calculation
540,000 / 20,000 = 27 seconds/item
Accordingly, to meet our customer demand, we’ll have to produce one item every 27 seconds, at a minimum. That, of course, if we take into account ideal production conditions. Meaning, in the situation where everything works perfectly and we will not have any seconds of downtime.
But, let’s face it, we all know that things don’t always work as we planned. Therefore, it would be wiser to run a bit faster than our Takt time and allow for some downtime.
However, that doesn’t mean we’re preparing for the worst. On the contrary, it means that we will be able to meet the delivery deadline even if something unforeseen occurs. Therefore, we choose to produce at a rate of 24 seconds/item. This will be the targeted Cycle time.
Download your free Takt time calculator
Cycle time
As we know from the Cycle time definition, this is the rhythm at which you are actually producing the item. To measure the frequency of items produced, we need to track the time between the completion of two items. Therefore, the period it takes from the output of one item to the output of the next item.
Let’s refer to the previous example. The time we had to produce each item to meet our customer demand was 27 seconds. This way, if we produce an item at 24 seconds, we’ll definitely fit into the 27 second Takt time. Besides, this will be possible even if there’ll be some unforeseen problems that will involve downtime.
Comparison
Cycle time = 24 sec < Takt time = 27 sec
(our production rate) (customer expectation)
Download your free Cycle time calculator
Lead time
As we already know, this is another dimension of the rhythm of our production process. It’s about how long it takes one item to make its way through your operation front to end.
To find out this interval we need to track the time for one item through the entire process. That is since it has entered the operation until it leaves the last step.Knowing this period, we will also have the opportunity to
- know how long our customer has to wait for his items to be completed. This is especially useful if our product is made to order.
- know how much inventory is between every step in our process. In this regard, the comparison between Takt time and Lead time is really helpful.
Example of Lead time calculation
Let’s suppose your small company produces personalized Flower-Cards. This is an operation that requires 3 work-steps. As a result, your company has allocated 3 employees, one for each Step.
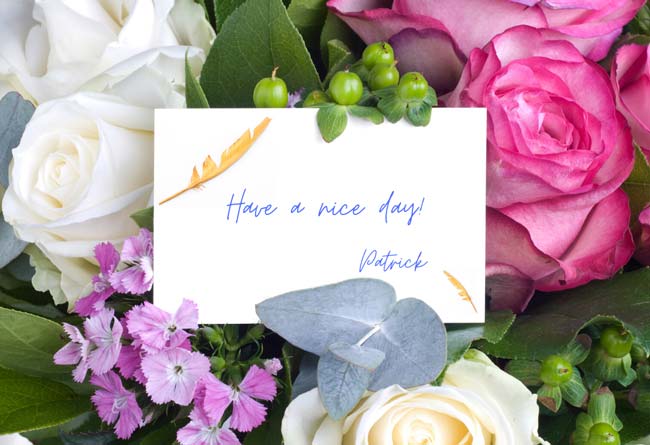
We assume that from Client M you have an order of 36,000 items a month.
As we said, the Takt time formula represents the available time divided by items needed. Thus, first of all, we need to calculate the available production time.Similar to the anterior example, let’s suppose that your company runs:
- a 7.5 hours shift
- one shift per day
- 20 days a month
Therefore, you’ll have 540,000 seconds available production time in a month.Accordingly, we can make the Takt time calculation: So, we need to divide 540,000 seconds by the number of items ordered. In your case, this is 36,000. Consequently, we’ll reach the result of 15 seconds.
Calculated Takt time
540,000 / 36,000 = 15 seconds / item
This means you will need to produce 1 item every 15 seconds. And this, your company has to do for 20 days a month, during the daily 7.5 hours shift. This is the minimum rhythm, necessary to meet your customer demand. This is your Takt time for Client M’s order.
Now, let’s suppose you timed the frequency with which an item is produced and obtained an average of 13 seconds.
Cycle time time measurement
Start→Step 1→Step 2→Step3→Stop
Cycle time = 13 sec < Takt time = 15 sec
(your production rate) (customer expectation)
Certainly, with this Cycle time, you will meet your customer demand. This is because your operation will produce an item every 13 seconds and your customer demands was 15 seconds.
But, let’s take a look at Cycle time, separately for each step. We’ll notice that:
- Preparing – Step 1, has an average of 6 seconds
- Laminating – Step 2 has an average of 13 seconds
- Packing – Step 3 has an average of 6 seconds
Now, we can see that the “Laminating” is slower than “Preparing” and “Packing”. Of course, overall we fit into the calculated Takt time. But, because step 2 is slower, a lot of inventory will accumulate before it. This is because the Step 1 employee prepares the cards faster than the Step 2 employee can laminate.
To improve this process, you could, for example, combine the first and the last step and still meet Takt time. 6 sec + 6 sec = 12 seconds, is still smaller than your Takt time which was calculated at 15 seconds.
Process improvement calculation
6 sec + 6 sec = 12 seconds < 15 seconds/ item
Step 1 Step2 Calculated Takt time
This requires Employee A to do Step 1 and then Step 2. That is, he has to put the customization element on the Flower-card and both in foil for lamination. After this, he has to put the previous laminated Flower-card in the envelope.
This will create a good balance between the work of the two employees. Moreover, there is no need for employee C to work on this project, which certainly leads to cost reductions.
So, let’s suppose you did just that. Thus, you have improved the production process and significantly reduced costs. Precisely for this reason, you receive another order from Customer P. He wants 36,000 items a month, each one completed in 30 seconds.
Therefore, you now have to produce 36,000 items per month for Client M, and 36,000 items for Client P. Specifically, that means 72,000 articles in total. As a result, you have a much higher workload and you need to calculate a new Takt time for this amount.
Takt time calculation for Client M + Client P orders
540,000 / 72,000 = 7.5 seconds/ item
In this situation, for the 3 Steps of the operation, you will have to double the number of employees. This means that you will allocate 2 employees for each Step. And, since the workflow presented above is efficient, it would be advisable to keep it. Therefore, you will create 2 work units, each one will be made up of Employee A + Employee B. And each employee will perform the steps set out above, namely:
- Unit 1: Employee A: Step1 Preparing + Step3 Packing & Employee B: Step 2 Laminating
- Unit 2: Employee A: Step1 Preparing + Step3 Packing & Employee B: Step 2 Laminating
Now, you need to measure the interval in which your operation produces an item. As before, each one of your 2 units produces one item every 13 seconds. That means your operations produce 2 items in 13 seconds. Therefore, for each item, the Cycle time is 6.5 seconds. Consequently, it falls within the Takt time of 7.5 seconds
Cycle time time measurement for Unit 1 & Unit 2
Cycle time = 6.5 sec < Takt time = 7.5 sec
(your production rate) (customer expectation)
Now let’s see what is the Lead time for your item. This way you will know for sure if for example Client P, will receive his item in 30 seconds, exactly as requested.
As we said before, this is a measurable size, so you will need to track the time for 1 item through the entire process. The result is 21 seconds, and that is enough to meet Customer P’s expectations.
Lead time measurement
Cycle time = 21 sec < Customer P’s SLA = 30 sec
(your production rate) (customer service-level agreement)
Anyway, if your Lead time is more than 30 seconds, then you’ll need to take action. You can review the entire operation process, to see where the inventory is accumulated.
Knowing these temporal dimensions of the production process helps us take the necessary measures to ensure the maximum performance of our production operation and to easily meet our customers’ expectations.